Phases of Pipeline Construction: An Overview
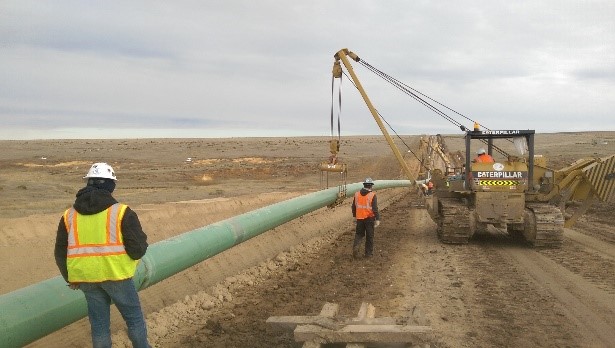
Planning for new capacity must begin far in advance of transporting the first barrel of oil, refined petroleum product, or first cubic foot of natural gas. Pipeline companies must determine possible routes for the new pipelines; acquire the right-of-way (ROW) to build, operate and maintain the pipelines; engineer the actual system designs; and construct the pipelines. Each of these steps are subject to rigorous regulatory reviews and approvals. Construction can only begin after the route selection receives regulatory approval, the ROW is obtained, and the system design is completed.
Regardless of the length of the pipeline, the construction process must be carefully planned to ensure the safety and integrity of the new pipeline and then executed to meet construction schedules and weather conditions. In some ways, installing a pipeline is much like an assembly-line process, with sections of the pipeline being completed in a sequence of repetitive steps.
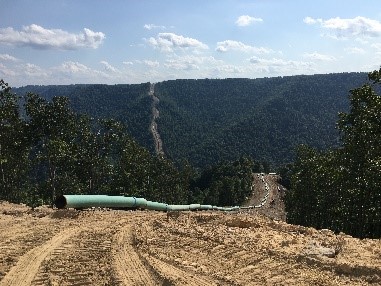
Pipeline construction requires a great deal of planning, consultation, and preparation. Companies must determine market demand and confirm customer support before investing in a project. Following the decision to move ahead with a project, the company must assess alternative routes for the pipeline, and select a final proposed route. Issues such as what communities need service; what size pipeline is needed; what natural resources might be impacted; what environmental areas and population centers might be intersected; and what other infrastructure systems lie along the route are just a few of the concerns considered.
The public and government agencies along the proposed route are also consulted, both individually and through public notices and public meetings. Extensive environmental and land use assessments are completed, and mitigation plans are formulated for various scenarios. These assessments may result in adjustments to the proposed pipeline route. Following final route selection, land is acquired by purchase, license or easement agreement, and permits are obtained from government agencies with jurisdictions along the right-of-way. Finally, multiple regulatory processes must be completed before the route is approved.
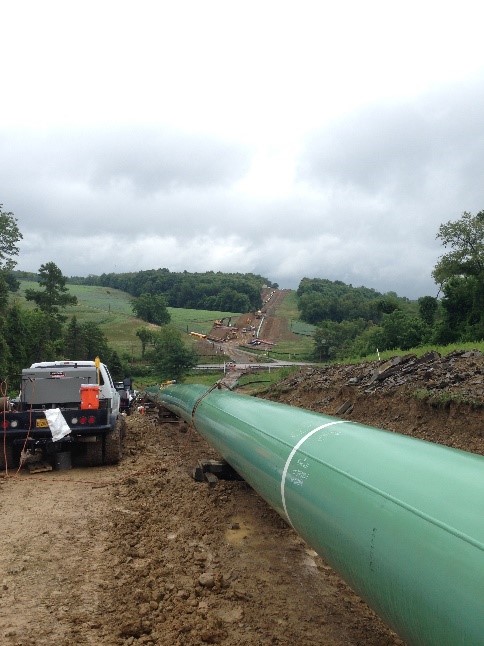
The Federal Energy Regulatory Commission (FERC), exercises regulatory control over siting and environmental approval of natural gas pipelines. Once a natural gas pipeline company proposes the primary route or location, it is examined and considered by FERC. The company must study and submit alternate routes or locations to avoid or minimize impacts to the environment, and then FERC, interested parties, or any commenter may suggest alternatives and modifications.
Effects on buildings, fences, crops, water supplies, soil, vegetation, wildlife, air quality, noise, safety, landowner interests, and more, are taken into consideration. FERC also considers whether a pipeline can be placed near or within an existing pipeline, power line, highway, or railroad right-of-way.
If a determination is made that the project will make no significant environmental impact, the project usually moves forward quickly. However, when it is determined that the project will make a significant environmental impact, a more in-depth environmental impact statement (EIS) must be developed and acceptable mitigation efforts reviewed and approved, prior to moving forward.
Federal regulatory approval is not ordinarily required for placement of new hazardous liquid pipelines, unless it crosses federal lands. Generally, state and local laws are the primary regulatory factors for siting of new hazardous liquid pipelines.
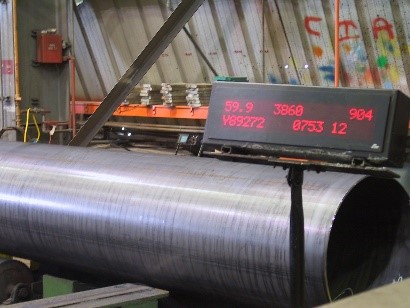
There are many significant differences between the design of hazardous liquid and natural gas transmission pipeline systems. These differences involve materials and components used, safety and environmental considerations, and a host of other design topics. A pipeline system may consist of various line pipe sizes, compressor or pump stations, control rooms, meter regulator stations, breakout tanks, storage facilities, and valves or other appurtenances. An entire transmission pipeline system may be very long in length, running from the coast of Texas to a major city in the Northeast, or it may be short, such as a lateral line from a production area to a refinery or processing facility. 49 CFR 192 and 49 CFR 195 prescribe the minimum federal design requirements for natural gas pipelines and hazardous liquid pipelines, respectively. State and local regulations may prescribe additional requirements beyond federal pipeline regulations.
Pipe sections are fabricated in steel rolling mills and inspected to assure they meet government and industry design and safety standards. Generally, sections are between 40 and 80 feet in length and are designed specifically for their intended location in the pipeline. A variety of soil conditions and geographic or population characteristics of the route will dictate different design requirements for pipe size, strength, wall thickness, and coating material.
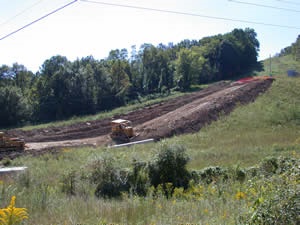
To prepare for construction, the selected route of the pipeline must be cleared. Construction work and equipment passage may require temporary work space be used that is outside the right-of-way. The temporary use of additional space is negotiated with the landowner. A survey crew carefully surveys and stakes the construction right-of-way to ensure only the pre-approved construction workspace is cleared. All potentially impacted utilities are located and marked to prevent damage during construction.
Next, to make the right-of-way a suitable work area, a clearing and grading crew prepares the route so the construction equipment can operate safely.
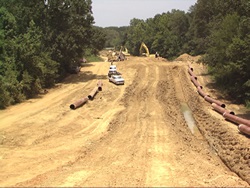
This crew removes trees, boulders, brush, and other impediments that may prohibit construction. This crew also prepares a working surface for the construction workers and equipment that will follow.
The site preparation crew installs silt fence along edges of streams and wetlands to prevent erosion of disturbed soil. Trees inside the right-of-way are cut down and the timber is removed or stacked alongside the right-of-way. Brush is commonly shredded or burned. Also, as may be necessary in agricultural areas, topsoil may be stripped to a predetermined depth and stockpiled along the sides of the right-of-way in cultivated areas to be returned to its original state, or better, during site restoration.
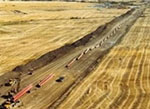
Once the construction right-of-way has been sufficiently cleared to allow construction equipment to gain access, sections of pipe are laid out along the right-of-way. This process is called 'stringing' the pipe.
Sections of pipe are designed and manufactured specifically for their intended locations along the pipeline. Locations along a pipeline system may have different requirements for pipe size, pipe strength and wall thickness, and coating material due to varying soil conditions, geographical features, or nearby population densities.
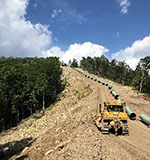
The pipe may be transported from the pipe mill to a pipe storage yard near the pipeline location or directly to the right-of-way. After the pipe is delivered to the right-of-way, a stringing crew will carefully distribute the various pipe sections per the design plan.
A trench is dug along the right-of-way to the surveyor’s specifications using wheel trenchers and backhoes. Topsoil is often removed from the work area and stockpiled on the non-working side of the trench to be used in site restoration. Occasionally, drilling and blasting are required to clear rock obstructions in a controlled manner.
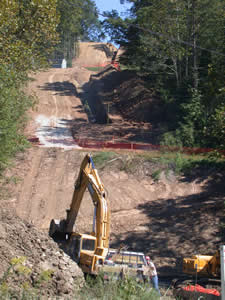
The trenches are dug deep enough to allow for an adequate amount of cover when the pipe is buried and wide enough to avoid coating damage during lowering-in operations. Federal regulations require that transmission pipelines be buried at least 30-inches below the surface in rural areas and deeper in more populated areas. The pipeline depth can vary depending on surrounding features. For example, at road crossings and crossings of bodies of water, the pipeline must be buried deeper. In other locations, such as when it is installed in consolidated rock the pipeline may lie in a shallower trench.
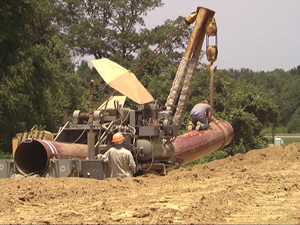
Pipe bends can be performed in the field or fabricated at an offsite facility. A bending machine is used to make slight bends in individual sections of the pipe. This allows the pipe to follow the pipeline route and to conform to the topography. The bending machine uses a series of clamps and hydraulic pressure to make a controlled bend in the pipe. All bending must be performed in strict accordance with federal regulations to ensure the integrity of the bend.
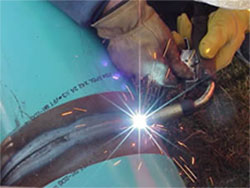
To carry out the welding process, the pipe sections are temporarily supported along the edge of the trench. The various pipe sections are then welded together into one continuous length or in segments via tie-in welds. This is accomplished using manual or mechanized welding procedures. All welding procedures must be qualified, and the welding of the pipe is controlled to strict specifications. Each weld procedure must be approved for use on the specific project in accordance with federal regulations.
Sidebooms are used to pick up, support, and align each section of pipe with the next section to make the first pass of each weld.
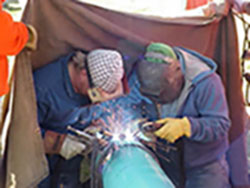
Each welder must pass qualification tests prior to welding on a pipeline project. Typically, each welder must successfully complete test welds using the same process of pipe welding to be used in the project. The welds are then evaluated by visual inspection, destructive testing, and non-destructive testing (NDT).
Weld quality is monitored throughout the project. To do this, qualified technicians use NDT methods (radiographs (X-rays) or ultrasound) to inspect the pipe welds to ensure the completed welds meet federally mandated quality standards. After evaluating the radiograph or ultrasonic images, the technicians interpret the NDT results. If the technician identifies any defects, the weld is either repaired and re-inspected or removed entirely.
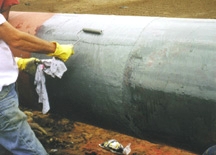
While a coating is applied to the pipe during manufacturing, the ends of the pipe remain uncoated to allow for welding. After the ends are welded together, the uncoated portion of pipe is thoroughly cleaned to remove any dirt or debris. A coating is then applied to prevent corrosion. Several different types of coatings may be used to coat field welds, such as two-part epoxy. After application, the coating must be cured per manufacturer’s specifications. Finally, entire coating of the pipe is inspected to ensure that it is free from defects before it is lowered into the ground.
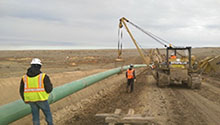
Once the pipeline is welded and coated, it is lowered into the trench using sidebooms and track hoes. The pipeline is lowered into the trench in a smooth and uniform manner to prevent overstressing and damaging the pipeline.
Care is taken to protect the pipeline and coating from damage caused by sharp rocks and abrasions as the backfill is placed into the trench. In areas where the ground is rocky and coarse, the backfill material is screened to remove rocks, or the pipeline is covered with a padding material to protect it from sharp rocks and abrasion.
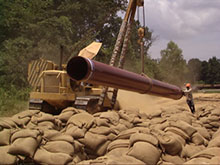
Alternatively, clean fill dirt may be brought in to cover the pipeline. As the backfill operations begin, the excavated material is returned to the trench in reverse order, with the subsoil put back first, followed by the topsoil. Once the pipe is sufficiently covered with the screened dirt or clean fill, the coarser soil and rock can then be used to complete the backfill. This ensures the topsoil is returned to its original position and site restoration can begin.
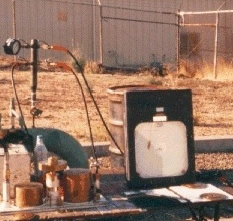
All newly constructed hazardous liquid and natural gas transmission pipelines must be pressure tested before they can be placed into service. The purpose of a pressure test is to find any defect that might threaten the pipeline's ability to sustain its designed maximum operating pressure, and allow these defects to be fixed before the pipe is placed into service. During a pressure test, the pipeline is filled with water, compressed air, or other gas and the internal pressure is raised to a specified level above the intended maximum operating pressure. Critical defects in the pipe will most likely fail during pressure testing. If the pipe does fail, these defects are repaired, or cut out, and the pressure test will be repeated to establish the maximum operating pressure of the pipeline.
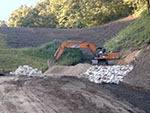
The construction right-of-way is restored as closely as possible to its original condition after pipeline completion. Depending on the location and circumstances, this could involve site restoration including replacing topsoil, repairing irrigation systems, applying fertilizer, grass seed, and other actions that may be necessary. The land owner is typically consulted on how they would like the right-of-way restored, however some restrictions apply. Site restoration is governed by local, state and federal agencies. PHMSA does not have jurisdiction over site restoration.
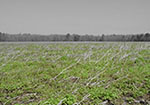
The right-of-way is carefully graded, and erosion-prevention measures are installed as necessary. Large stones, known as "riprap", or other methods are sometimes installed to prevent erosion, stabilize soils, and retain habitat following construction.